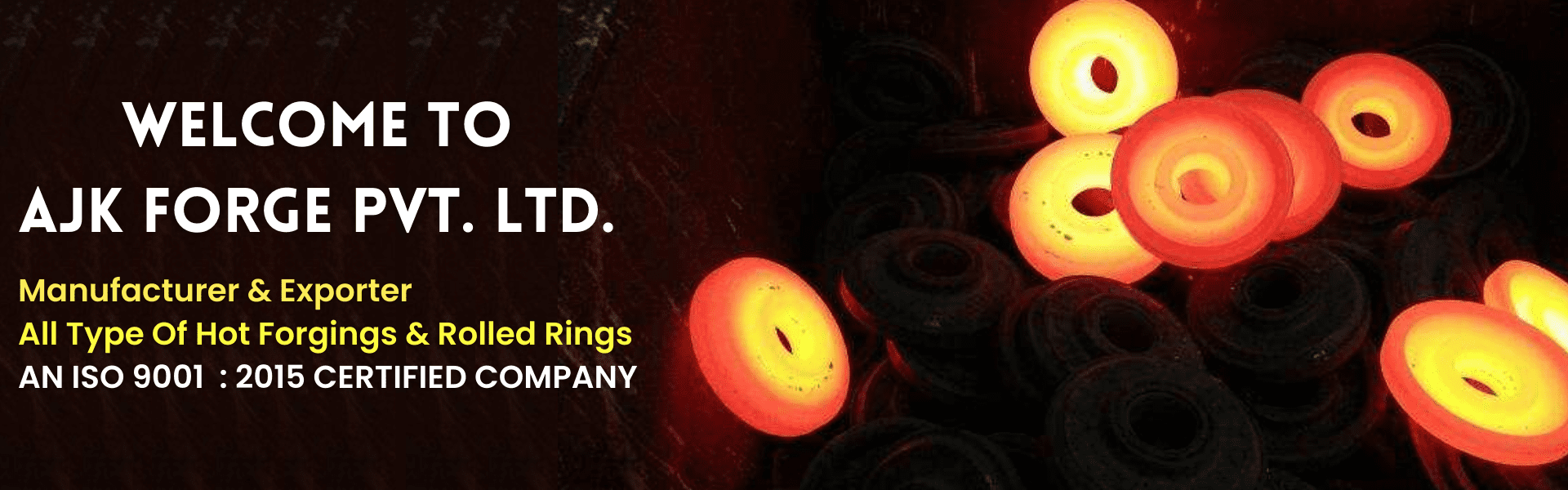
About Us
AJK FORGE PVT. LTD. is one of the leading manufacturers of closed die steel forgings & forged Rolled rings situated in Industrial Zone of Veraval (Shapar) 15 kms from Rajkot city in Gujarat state. We specialize in all types of drop forgings & forging Rings as per customer specifications in carbon steel, alloy steel & stainless steel and supply them in forged, heat treated, premachined or fully machined condition.
AJK FORGE PVT. LTD is managed by well experienced & qualified professionals having 10 years experience in forging unit. Our company is ISO-9001-2015 Certified by TUV SUD South Asia Pvt Ltd.
We are manufacturing various types of forging components like forging rings, Synchro Rings, Spacer rings, Bearing rings, End Rings for Submersible Pumps for V3,V4,V6 & V8,Gears, Gear Blanks, Connecting rods, Camshafts, Forks, Yokes, Flanges & pipe fittings and Other Transmission Components.
We have got Drop forging as well as ring rolling Facility available at our plants. Our production capacity is 300 Metric tons per Month. Our company has well equipped die shop, forge shop & machine shop. The job capacity in Ring Rolling is upto 300 mm outer diameter (OD), 60 mm Height & 10 Kg weight while in case of drop forging upto 20 kgs per piece.
We are indirect regular OE suppliers to Tata Motors Ltd & Mahindra & Mahindra Ltd.
We are also regular OEM Suppliers to Submersible pumpset manufacturers.
Our production facilities have been designed in such a way that all the manufacturing facilities are under one roof. The forge shop as well as die shop is equipped with EOT cranes to shift the material from place to place.
Raw material incoming from the approved steel mills are kept in the stockyard and 100% visual examination is done.As per customer’s requirement physical & chemical testing is done. After approval of the material, the material is send to cutting section for cutting. In cutting section as per cut weight given the material is cut.
Die is made as per customer’s sample or drawing of AJK which is approved by the customer. Plaster is taken out from the die & layout inspection of the plaster cast is carried out & inspection report is made for future reference.
In forge shop, continous production is achieved by pusher furnace in which temperature is controlled by temperature controller. Hot inspection is carried out at regular intervals.Inprocess inspection is carried out at regular intervals to check deviation of dimension from the control plan.
All the forged products are then sent for heat treatment as per customer’s requirement. Then shot blasting is carried out and final inspection is carried out as per control plan. Also the forging is checked 100% visually for scale pit, unfilling etc to avoid rejection at customer’s end.
As per customers requirement packing of the components and dispatch is done.
Our Products
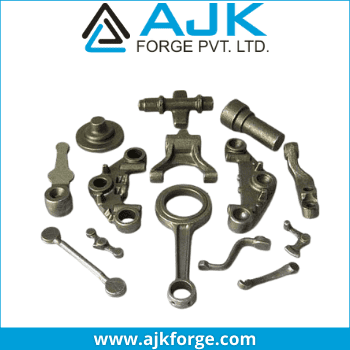
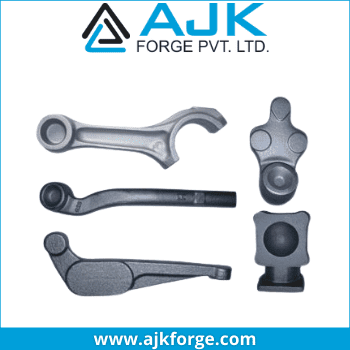
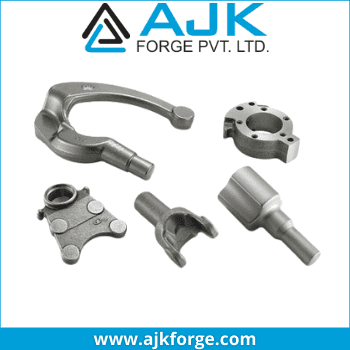
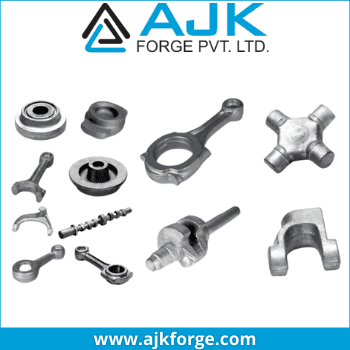
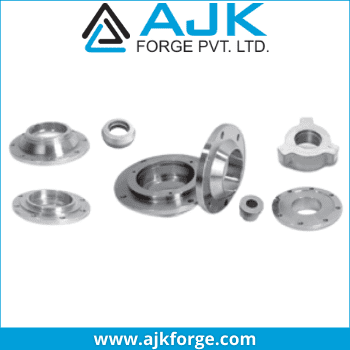
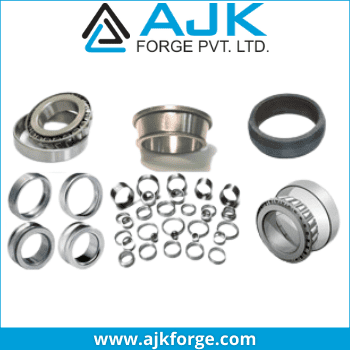
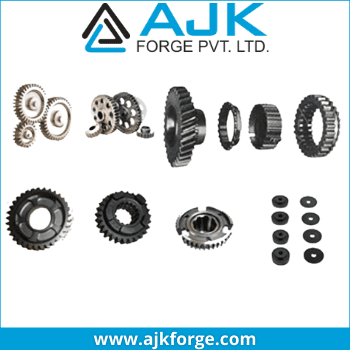
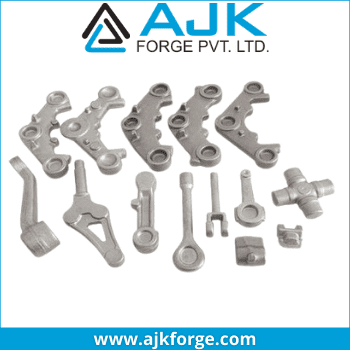
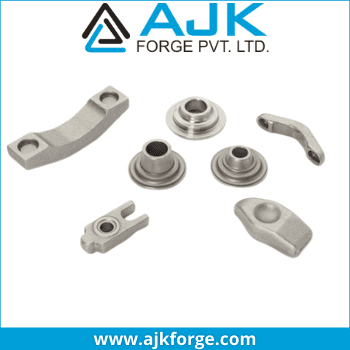
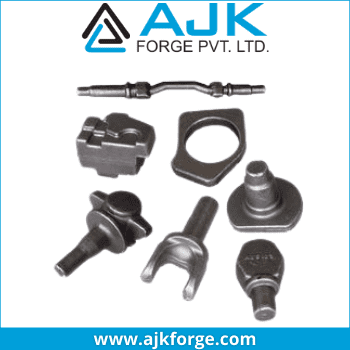
Tell us your Idea
We will get back to you in less than 24 hours.